Heat Treatment Process Pdf Free Download
In this article, you learn what is the heat treatment process? Its methods, types, and the purpose, procedure, application of heat treatment. Heat treatment is an essential operation in the manufacturing process of machine parts and tools.
What is Heat Treatment?
Heat treatment is defined as an operation involving the heating and cooling of a metal or an alloy in the solid-state to obtain certain desirable properties without change composition.
The process of heat treatment is carried out to change the grain size, to modify the structure of the material, and to relieve the stresses set up the material after hot or cold working.
- The heat treatment is done to improve the machinability.
- To improve magnetic and electrical properties.
- To increase resistance to wear, heat and corrosion, and much more reason.
Heat treatment consists of heating the metal near or above its critical temperature, held for a particular time at that finally cooling the metal in some medium which may be air, water, brine, or molten salts. The heat treatment process includes annealing, case hardening, tempering, normalizing and quenching, nitriding, cyaniding, etc.
Types of Heat Treatment Processes
Following are the different types of heat treatment processes:
- Annealing
- Normalizing
- hardening
- Tempering
- Nitriding
- Cyaniding
- Induction Hardening
- Flame Hardening
Read Also:
- What is Metal Casting Process? A Complete guide
- List of Mechanical Properties of materials
Types of Heat Treatment
1. Annealing
Annealing is one of the most important processes of heat treatment. It is one of the most widely used operations in the heat treatment of iron and steel and is defined as the softening process.
Heating from 30 – 50°C above the upper critical temperature and cooling it at a very slow rate by seeking it the furnace. The main aim of annealing is to make steel more ductile and malleable and to remove internal stresses. This process makes the steel soft so that it can be easily machined.
1.1 Purpose of Annealing
- It softens steel and to improve its machinability.
- To refine grain size and remove gases.
- It removes the internal stresses developed during the previous process.
- To obtain desired ductility, malleability, and toughness.
- It modifies the electrical and magnetic properties.
1.2 Procedure for Annealing
Depending on the carbon content, the steel is heated to a temperature of about 50° to 55°C above its critical temperature range. It is held at this temperature for a definite period of time depending on the type of furnace and nature of work. The steel is then allowed to cool inside the furnace constantly.
1.3 Application of annealing
It is applied to castings and forgings.
2. Normalizing
Normalizing: The main aim of normalizing is to remove the internal stresses developed after the cold working process. In this, steel is heated 30 – 50°C above its upper critical temperature and cooling it in the air.
It improves mechanical and electrical properties, machinability & tensile strength. Normalizing is the process of heat treatment carried out to restore the structure of normal condition.
2.1 Purpose of Normalizing
- Promote uniformity of structure.
- To secure grain refinement.
- To bring about desirable changes in the properties of steel.
2.2 Procedure for Normalizing
The steel is heated to a temperature of about 40° to 50°C above its upper critical temperature. It is held at this temperature for a short duration. The steel is then allowed cool in still air at room temperature, which is known as air quenching.
2.3 Application of Normalizing
- It is applied castings and forgings to refine grain structure and to relieve stresses.
- It is applied after cold working such as rolling, stamping and hammering.
3. Hardening
Hardening: The main aim of the hardening process is to make steel hard tough. In this process, steel is heated 30° – 40°C above the upper critical temperature and then followed by continues cooling to room temperature by quenching in water or oil. It is the opposite process of annealing.
3.1 Purpose of Hardening
- By hardening, it increases the hardness of steel.
- To resist to wear
- Allows the steel to cut other metals
3.2 Procedure for Hardening
The steel is heated above its critical temperature range. It is held at that temperature for a definite period of time. The steel is then rapidly cooled in a medium of quenching.
The quenching medium is selected according to the degree of hardness desired. The air, water, bring, oils and molten salts are used as quenching mediums. A thin section such knife blades are cooled in air. Water is widely used medium but it results in the formation of bubbles on the surface of the metal.
Hence brine solution is used to prevent this. Oil is used when there is a risk of distortion on cracks and is suitable for alloy steels. The molten salts are used to cool thin section to obtain crack-free and impact-resistant products.
3.3 Application of Hardening
It is applied for chisels, sledgehammer, hand hammer, centre punches, taps, dies, milling cutters, knife blades and gears.
4. Tempering
Tempering: When the hardening process hardens a steel specimen, it becomes brittle and has high residual stress. It is an operation used to modify the properties of steel hardened by quenching for the purpose of increasing its usefulness.
Tempering or draw results in a reduction of brittleness and removal of internal strains caused during hardening. Steel must be tempered after the hardening process.
The tempering is divided into three categories according to the usefulness of steel required.
- Low-temperature tempering.
- Medium temperature tempering.
- High-temperature tempering.
4.1 Purpose of Tempering
- To relieve internally stressed caused by hardening.
- To reduce brittleness.
- Improve ductility, strength and toughness.
- To increase wear resistance.
- To obtain desired mechanical properties.
4.2 Procedure for Tempering
The steel after being quenched in the hardening process is reheated to a temperature slightly above the temperature range at which it is to be used, but below the lower critical temperature. The temperature here varies from 100°C to 700°C.
The reheating is done in a bath of oil or molten lead or molten salt. The specimen is held in the bath for a period of time till attains the temperature evenly, the time depends on the composition and desired quality of steel. Now the specimen is removed from the bath and allow to cool slowly in still air.
4.3 Application of Tempering
It is applied to cutting tools, tools, and gears, which are hardened by the hardening process.
5. Nitriding
Nitriding is the process of the case or surface hardening in which nitrogen gas is employed to obtain hard skin of the metal. In this process, steel is heated in the presence of ammonia environment.
Due to this, a nitrogen atom is deposited and makes material hard. Induction hardening and Flame hardening objects are heated by an oxy-acetylene flame.
5.1 Purpose of Nitriding
- To harden the surface of the steel to a certain depth.
- Increase resistance to wear and fatigue.
- To increase corrosion resistance.
5.2 Procedure for Nitriding
It is done in the electric furnace where temperature varying between 450° and 510°C is maintained. The part is well machined and finished and placed in an airtight container provided with outlet and inlet tubes through which ammonia gas is circulated.
The container with the part is placed in the furnace and ammonia gas is passed through it while the furnace is heated.
During the process of heating nitrogen gas is released from ammonia in the form of atomic nitrogen, which reacts with the surface of the part, and forms iron nitrate.
The depth of entrance depends upon the length of time spent at the nitriding temperature. The part is taken out and it does not require any quenching or further heat treatment.
5.3 Application of Nitriding
- It is applied for hardening the surface of medium carbon alloy steels.
6. Cyaniding
Cyaniding: In this process, steel is heated in the presence of sodium cyanide environment. Due to this, carbon and nitrogen atoms are deposited on the surface of steel and make it hard.
6.1 Purpose of Cyaniding
- This method is effective for increasing the fatigue limit of medium and small-sized parts such as gears, shafts, wrist pins etc.
- To increase surface hardness.
- increase wear resistance.
- To give the clean, bright and pleasing appearance to the hardened surface.
6.2 Produce for Cyaniding
The parts to be treated is dipped in a molten cyanide salt bath maintained at a temperature of 950°C. The molten salts used are sodium chloride, sodium carbonate, sodium cyanide and soda ash.
The immersed article is left in the molten cyanide salt at a temperature of 950°C for about 15 to 20 minutes. The decomposition of sodium cyanide yield nitrogen and carbon from carbon monoxide, which is diffused into the surface resulting in hardening the surface. The part is then taken out of the bath and quenched in water or oil.
6.3 Application of Cyaniding
- It is applied to small articles like gears, bushing, screws, pins and small hand tools, which require a thin and hard wear-resisting surface.
7. Carburising
Carburising: In this process, steel is heated in the presence of carbon environment. Due to this carbon atoms are deposited on the metal surface and make it hard.
8. Case Hardening or Surface Hardening
The main aim of this process is to make the only external surface of steel hard and inner core soft. It is the process of carburisation i.e., saturating the surface layer of steel with carbon, or some other process by which case is hardened and the core remains soft.
8.1 Purpose of Case Hardening
- To obtain a hard and wear resistance to machine parts.
- By case hardening, it obtains a tough core.
- To obtain a higher fatigue limit and high mechanical properties in the core.
Purpose of Heat Treatment of Steel
The following are the purposes of heat treatment.
- To improve mechanical properties such as tensile strength, hardness, ductility, shock resistance, and resistance to corrosion.
- Improve machinability.
- To relieve the internal stresses of the metal-induced during cold or hot working.
- To change or refine grain size.
- Improve magnetic and electric properties.
- Increase resistance to wear, and corrosion.
- To increase the surface hardness.
Download Pdf of this article
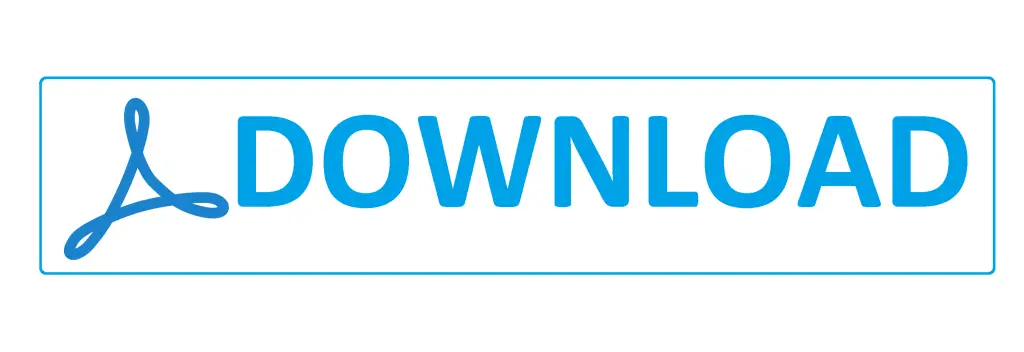
Conclusion
So now, we hope that we have clear all your doubts about Heat Treatment Process. If you have still any doubts about the Heat Treatment Process or methods, types, applications you can ask in the comments.
We have also a Facebook community for you guys. If you want, you can join our community, here is the link to our Facebook group.
That's it thanks for reading. If you like our article then please share it with your friends. If you have any questions about any topic you can ask in the comment section.
Subscribe to our newsletter to get notified when we upload new posts.
Read More About Mechanical Engg on our Site:
- Properties and Types of Moulding Sand
- Cast Iron: Types, Properties And Effects of Impurities
- List of 20 Different Types of Nuts and Bolts
Source: https://www.theengineerspost.com/heat-treatment-of-steel/
Posted by: tomtomauberowe0267001.blogspot.com
Post a Comment for "Heat Treatment Process Pdf Free Download"